Le contrôle commande est un élément fondamental de l’automatisation industrielle. Il assure la surveillance, la coordination et la régulation des processus de production ou des infrastructures techniques. Grâce à lui, les machines et systèmes fonctionnent de manière optimale, sécurisée et efficace.
Que ce soit dans les usines, les centrales électriques, les transports ou les bâtiments intelligents, le contrôle commande joue un rôle clé pour garantir la performance et la fiabilité des installations. Avec l’essor de l’Industrie 4.0, il évolue en intégrant des technologies comme l’Internet des objets (IoT), l’intelligence artificielle (IA) et la maintenance prédictive.
Dans cet article, nous allons explorer en détail les principes, les composants, les applications, ainsi que les défis et opportunités liés au contrôle commande.
Contenu de l'Article
Qu’est-ce que le Contrôle Commande ?
Le contrôle commande peut être défini comme l’ensemble des dispositifs matériels et logiciels chargés d’effectuer deux fonctions principales : contrôler et commander. Ces deux actions sont intimement liées et reposent sur une boucle d’information en temps réel :
Le contrôle: Il consiste à mesurer l’état d’un processus industriel ou d’une installation à l’aide de capteurs. Ces capteurs collectent en continu des données sur des grandeurs physiques (température, pression, débit, niveau, vitesse, position, etc.) ou des états logiques (capteur de présence, indicateur d’ouverture/fermeture, etc.). Les mesures obtenues permettent de déterminer si le processus se déroule conformément aux spécifications et aux consignes définies au préalable (exemple : température de consigne, vitesse de rotation souhaitée).
La commande: Elle s’exerce une fois que l’analyse des données collectées a été réalisée. Si un écart ou une anomalie est détecté entre l’état mesuré et l’état souhaité, le système de contrôle-commande émet des signaux de commande à l’intention d’actionneurs (moteurs, vannes, relais, etc.). Ces actionneurs vont alors ajuster le fonctionnement du système afin de ramener le processus vers sa consigne optimale ou de réagir à un événement imprévu.
L’objectif fondamental du contrôle commande est donc de maintenir un processus dans un état stable et performant, tout en assurant la sécurité et la qualité. Il s’agit d’une fonction critique dans toutes les installations automatisées : qu’il s’agisse d’une ligne de production manufacturière, d’une centrale électrique ou d’un système de transport ferroviaire, le contrôle-commande veille à ce que les consignes soient respectées et les dérives maîtrisées.
Les Composants du Contrôle Commande
Pour assurer ce double rôle de contrôle et de commande, les systèmes de contrôle commande s’appuient sur plusieurs types de composants complémentaires, organisés en une architecture souvent hiérarchisée :
Capteurs
Les capteurs sont la première porte d’entrée d’informations dans le système de contrôle commande. Ils mesurent des paramètres physiques ou logiques du processus : température, pression, taux d’humidité, position d’un objet, niveau d’un liquide, etc. Sans capteurs, il serait impossible de surveiller l’état réel du système. Leur précision et leur fiabilité sont donc primordiales pour garantir la qualité de l’automatisation.
Automates programmables industriels (API ou PLC)
Aussi appelés « cerveaux » du système, les automates programmables industriels exécutent en boucle des programmes logiques ou algorithmes de contrôle. Ils reçoivent les signaux issus des capteurs, comparent ces valeurs aux consignes, et en cas d’écart, génèrent des ordres de commande. Ces automates sont spécialement conçus pour fonctionner en environnement industriel contraint (température, humidité, vibrations), avec une grande robustesse et une fiabilité élevée.
Actionneurs
Les actionneurs traduisent en actions concrètes les décisions prises par les automates. Ils peuvent prendre la forme de vannes pilotant le passage d’un fluide, de moteurs contrôlant un mouvement, de relais électriques commutant un courant, ou encore de vérins pneumatiques. Les actionneurs exécutent fidèlement les ordres reçus pour corriger un écart ou maintenir un état donné.
Interfaces Homme-Machine (IHM)
Les IHM permettent aux opérateurs humains de surveiller et d’interagir avec le système de contrôle commande. Elles prennent souvent la forme d’écrans tactiles, de pupitres de commande ou de logiciels de supervision accessibles via un ordinateur. Grâce à ces interfaces, il est possible de visualiser en temps réel l’état du processus, de régler certains paramètres, de lancer des séquences particulières ou encore de diagnostiquer les éventuelles pannes.
Systèmes SCADA (Supervisory Control And Data Acquisition)
Les SCADA constituent la couche de supervision globale, collectant et centralisant les données issues de l’ensemble des capteurs et automates. Ils offrent une vue d’ensemble du processus, sous forme de graphiques, de tableaux de bord, d’alarmes et d’historiques. Les opérateurs peuvent ainsi contrôler et diagnostiquer des installations complexes à distance, en bénéficiant d’une vision globale et synthétique. Les SCADA sont souvent utilisés dans de grandes infrastructures (réseaux d’énergie, usines de traitement de l’eau, etc.) pour coordonner des centaines, voire des milliers de points de mesure et de commande.
Comment Fonctionne un Système de Contrôle-Commande ?
Le fonctionnement d’un système de contrôle commande se conçoit généralement sous forme de boucle fermée, qui peut être décrite en plusieurs étapes successives :
Acquisition des données
Les capteurs disséminés dans l’installation relèvent en continu des valeurs physiques ou logiques. Par exemple, un capteur de température signale que la température actuelle est de 25 °C, tandis qu’un capteur de pression indique 2 bars. Ces informations sont transmises aux automates programmables via un réseau industriel ou des liaisons câblées.
Analyse et traitement
L’automate compare les valeurs mesurées à des consignes définies au préalable. Ces consignes correspondent à l’objectif optimal de fonctionnement (exemple : maintenir une température entre 20 et 22 °C). Si l’on détecte un écart, l’automate enclenche la suite de la séquence de commande.
Prise de décision
Sur la base de la logique de contrôle programmée (souvent via un langage spécifique aux automates, comme le Ladder ou le langage structuré), l’automate décide de l’action à entreprendre. Cela peut être, par exemple, d’ouvrir une vanne de refroidissement ou de démarrer un moteur pour activer un système de ventilation.
Action et ajustement
Les ordres de l’automate sont transmis aux actionneurs qui exécutent physiquement l’ajustement. Ainsi, si la pièce est trop chaude, l’actionneur déclenche le système de climatisation jusqu’à ce que la température soit de nouveau conforme à la consigne.
Supervision et retour d’information
En parallèle, un système SCADA ou une IHM permet à l’opérateur de surveiller l’état du processus. Les valeurs de température, de pression, de débit, etc., s’affichent sur des écrans en temps réel. L’opérateur peut intervenir manuellement si nécessaire, par exemple en modifiant une consigne ou en déclenchant un arrêt d’urgence.
Cette boucle se répète en continu, offrant une réactivité élevée qui est la clé de la performance dans la plupart des processus industriels. Chaque cycle de contrôle commande peut être très rapide (de l’ordre de la milliseconde) ou plus lent, selon la nature du procédé et les contraintes de réactivité ou de sécurité associées.
Applications du Contrôle-Commande
Le contrôle commande est au cœur de l’automatisation de nombreux secteurs d’activité. Parmi les applications notables, on retrouve :
Industrie manufacturière
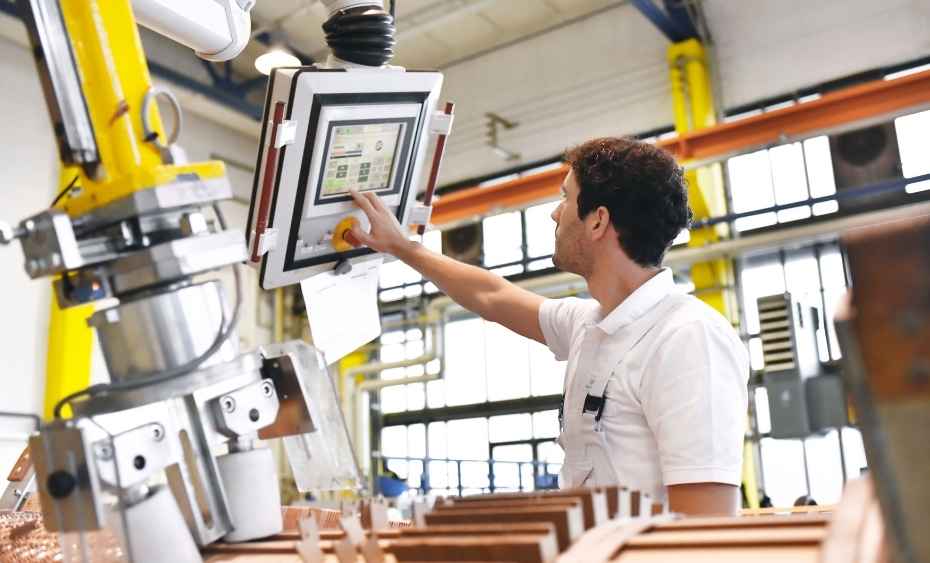
Dans les chaînes de production automatisées, le contrôle commande régule la cadence des machines, contrôle la qualité des pièces fabriquées et coordonne les différentes étapes de transformation. Par exemple, dans l’industrie automobile, les robots qui soudent les carrosseries ou qui peignent les véhicules sont pilotés par des systèmes de contrôle commande sophistiqués, garantissant une précision et une rapidité inégalées.
Énergie

Dans les centrales électriques (thermiques, nucléaires, hydrauliques, éoliennes, etc.), le contrôle commande assure la régulation du débit, de la pression ou encore de la charge de production. Il coordonne également la distribution d’énergie sur le réseau, en s’assurant que l’offre et la demande restent en équilibre. Les systèmes SCADA sont particulièrement présents dans la gestion des réseaux d’énergie, permettant une supervision à distance de postes électriques disséminés sur un vaste territoire.
Transports

Les systèmes de signalisation ferroviaire, les lignes de métro automatisées et les feux de circulation routiers reposent sur du contrôle commande pour garantir la fluidité et la sécurité du trafic. Les métros automatiques, par exemple, ajustent en temps réel la vitesse, l’ouverture/fermeture des portes et la distance entre chaque rame grâce à des boucles de contrôle-commande extrêmement fiables.
Bâtiments intelligents (Smart Buildings)
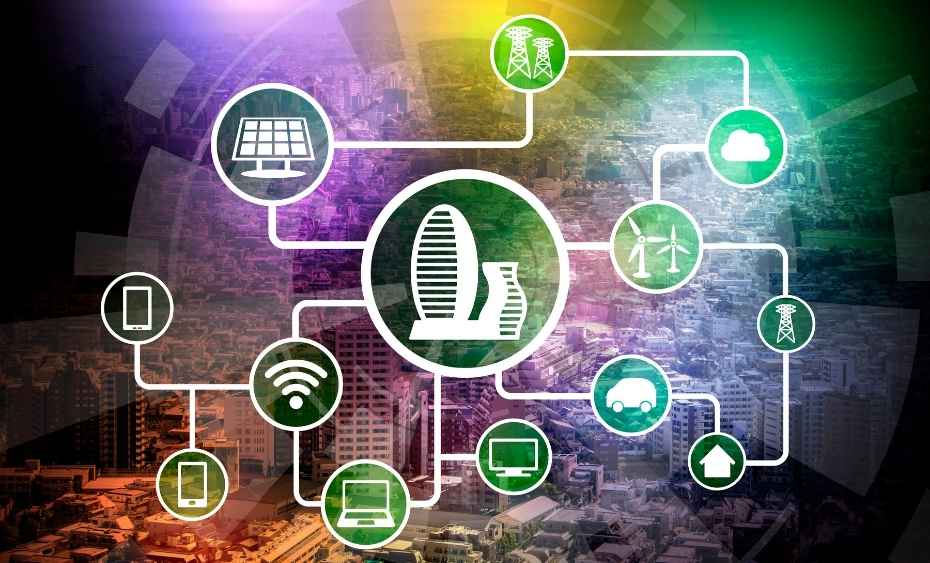
Dans la gestion technique d’un bâtiment, le contrôle commande gère la climatisation, le chauffage, la ventilation, l’éclairage et parfois même la sécurité (détection incendie, contrôle d’accès). Cela permet d’optimiser les consommations d’énergie et d’offrir un meilleur confort aux occupants. Les bâtiments dits « intelligents » intègrent de plus en plus de capteurs pour ajuster automatiquement leurs paramètres en fonction de l’occupation réelle et des conditions extérieures.
Traitement de l’eau
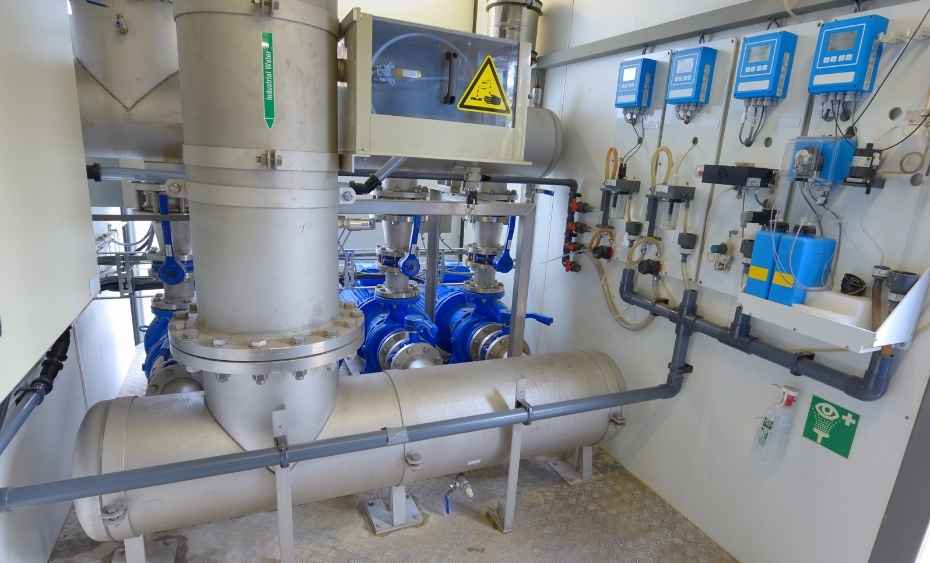
Les stations d’épuration et les usines de dessalement utilisent des systèmes de contrôle commande pour réguler les flux d’eau, la qualité de filtration, la distribution de produits chimiques, ou encore la gestion des bassins de décantation. Là encore, la supervision à distance facilite le suivi continu de la qualité de l’eau, élément critique pour la santé publique.
Dans tous ces domaines, la finalité reste la même : assurer en permanence le bon déroulement du processus, prévenir les dysfonctionnements et optimiser la performance globale. Le contrôle commande offre un niveau de précision et de fiabilité indispensable pour les opérateurs et les gestionnaires de systèmes complexes.
Avantages du Contrôle Commande
La mise en place d’un système de contrôle commande s’accompagne de multiples bénéfices pour les entreprises et les organismes concernés :
Amélioration de la productivité
En automatisant une partie ou la totalité d’un processus, le contrôle commande permet de réduire les temps d’arrêt et de maximiser les débits de production. Les cycles de contrôle rapides détectent aussitôt les dérives et ajustent la production en conséquence, évitant ainsi les goulots d’étranglement et la production de lots non conformes.
Sécurité accrue
Les systèmes de contrôle commande sont conçus pour détecter les anomalies et déclencher des alarmes ou des actions correctives quasi instantanément. Dans des environnements critiques (centrales nucléaires, sites chimiques), ils contribuent grandement à éviter les accidents industriels. La présence de boucles de sécurité dédiées (Safety Instrumented Systems) est souvent couplée au contrôle-commande afin de prévenir tout risque majeur.
Qualité constante
Grâce à une régulation précise des paramètres de fabrication, le contrôle commande permet de maintenir une qualité homogène dans le temps. Les écarts de production sont minimisés, les marges de tolérance sont mieux respectées et la traçabilité est grandement facilitée. Cela est essentiel dans des secteurs tels que l’agroalimentaire, la pharmacie ou l’aéronautique, où la conformité aux normes est cruciale.
Efficacité énergétique
L’optimisation en continu du fonctionnement des machines contribue à réduire la consommation d’énergie, qu’il s’agisse d’électricité, de gaz, d’eau ou d’autres ressources. Par exemple, dans une installation de chauffage, le contrôle-commande peut ajuster en temps réel la puissance de chauffe selon la température extérieure ou le taux d’occupation des lieux, évitant ainsi les surconsommations inutiles.
Supervision à distance
Les systèmes SCADA et les IHM modernes offrent la possibilité de piloter des installations dispersées depuis un poste centralisé, voire depuis des terminaux mobiles. Cela réduit les coûts liés à la présence physique de personnels sur chaque site et accélère la réactivité en cas de problème. La supervision à distance est particulièrement avantageuse pour les infrastructures étendues (réseaux de transport, pipeline, parcs éoliens, etc.).
Maintenance facilitée
Le contrôle commande stocke des historiques de fonctionnement (logs, alarmes, tendances). Cette base de données est une source précieuse pour réaliser des diagnostics de panne ou programmer des opérations de maintenance préventive. Certains systèmes vont plus loin en intégrant des algorithmes de maintenance prédictive, capables d’anticiper l’usure ou la défaillance de composants critiques.
Les Enjeux Actuels et Futurs du Contrôle-Commande
À l’heure de l’Industrie 4.0, le contrôle commande se trouve en pleine mutation, stimulée par l’émergence de nouvelles technologies numériques et d’exigences toujours plus élevées en matière de compétitivité et de durabilité. Parmi les tendances et enjeux majeurs, on peut citer :
Internet des Objets (IoT) et Big Data
Le déploiement massif de capteurs connectés (IoT) multiplie le volume de données collectées en temps réel. Ceci offre une meilleure granularité dans la surveillance des processus et ouvre la voie à des analyses de données avancées. Les technologies de Big Data, combinées aux plateformes de cloud computing, permettent de traiter ces informations à grande échelle, pour une optimisation fine du contrôle-commande.
Intelligence Artificielle (IA)
L’IA appliquée au contrôle commande promet des systèmes auto-apprenants capables de s’adapter en permanence à des conditions changeantes et d’améliorer leur propre performance. Des algorithmes de machine learning peuvent, par exemple, détecter des signaux faibles annonciateurs d’une défaillance, ou encore ajuster automatiquement les paramètres de production pour maximiser la qualité ou l’efficacité énergétique.
Cybersécurité
La digitalisation croissante des installations industrielles et leur interconnexion avec des réseaux IP (Internet) exposent les systèmes de contrôle commande à des risques de cyberattaques. La protection des infrastructures critiques est devenue un enjeu stratégique. Des solutions de sécurisation des automates, de chiffrement des communications et de détection d’intrusion font désormais partie intégrante de l’architecture de contrôle-commande.
Maintenance prédictive
Au-delà de la maintenance préventive classique, la maintenance prédictive repose sur l’analyse de données collectées en continu pour anticiper les pannes et planifier les interventions au moment optimal. Cela permet de réduire drastiquement les coûts de maintenance et les interruptions non planifiées de la production. Les outils de maintenance prédictive s’appuient souvent sur des technologies d’IA et sur l’intégration étroite avec le système de contrôle-commande.
Normes et standards d’interopérabilité
Avec la multiplication des fournisseurs, des capteurs et des protocoles de communication, l’interopérabilité devient cruciale. Des standards ouverts, comme OPC UA (Open Platform Communications Unified Architecture), encouragent la compatibilité entre équipements et facilitent l’intégration de nouvelles composantes dans l’architecture de contrôle commande.
Développement durable et transition énergétique
Les préoccupations environnementales poussent de plus en plus d’industriels à optimiser leurs consommations de ressources (eau, énergie) et à réduire leurs émissions de CO₂. Le contrôle-commande, en pilotant avec précision les équipements, contribue à la mise en œuvre de stratégies durables, que ce soit pour la production d’énergie renouvelable ou pour l’amélioration de l’efficacité énergétique dans les usines.
Grâce à ces évolutions, le contrôle commande s’oriente vers des solutions toujours plus intelligentes, communicantes et fiables. Les industriels qui adoptent ces technologies avancées peuvent gagner un avantage concurrentiel significatif, en améliorant la performance globale de leurs opérations tout en maîtrisant leurs coûts et leur impact écologique.
Conclusion : Un Pilier Incontournable de l’Industrie Moderne
Le contrôle commande est la colonne vertébrale de l’automatisation industrielle. Il assure la performance, la sécurité et la qualité des processus tout en optimisant les coûts et la consommation énergétique.
Grâce aux technologies émergentes, il devient plus intelligent, flexible et sécurisé. Pour les entreprises industrielles, investir dans un système de contrôle commande performant n’est plus une option, mais un levier stratégique pour rester compétitives à l’ère de l’Industrie 4.0.
Vous souhaitez moderniser votre système de contrôle-commande ?
Contactez nos experts pour une solution sur mesure et découvrez comment l’automatisation peut transformer vos processus industriels.
FAQ sur le Contrôle-Commande
Qu’est-ce qu’un système de contrôle commande ?
Un système de contrôle-commande est un ensemble de dispositifs matériels et logiciels permettant de surveiller, réguler et piloter un processus industriel. Il repose sur des capteurs pour collecter des données, des automates pour analyser ces informations, et des actionneurs pour ajuster le processus en temps réel.
Que signifie contrôle commande ?
Le contrôle consiste à mesurer les paramètres d’un processus (température, pression, débit) grâce à des capteurs.
La commande intervient lorsque le système détecte un écart par rapport à la consigne. L’automate envoie alors un ordre aux actionneurs pour corriger la situation.
Quels protocoles de communication sont utilisés dans les systèmes de contrôle commande ?
Les protocoles courants incluent Modbus, Profibus, EtherNet/IP, et OPC UA, permettant aux équipements de communiquer entre eux.